Custom Sheet Metal Cutting
- Sheet metal cutting is a subtractive process, where material is removed to create parts with desired shapes and dimensions.
- Our cutting ability ranges from mechanical cutting to thermal and waterjet cutting, suitable for various metal sheets and plates, and following post-cutting process and strict quality controls.
- Various Cutting Methods
- Hiqh Quality Post-cutting Process
- Strict Quality Controls
- Suitable for Almost Metals
Our Cutting Techniques
Three of the most common methods for cutting sheet metal are laser cutting, plasma cutting, and waterjet cutting. Choosing the right sheet metal cutting technique depends on various factors, including material type, thickness, desired edge quality, and budget.
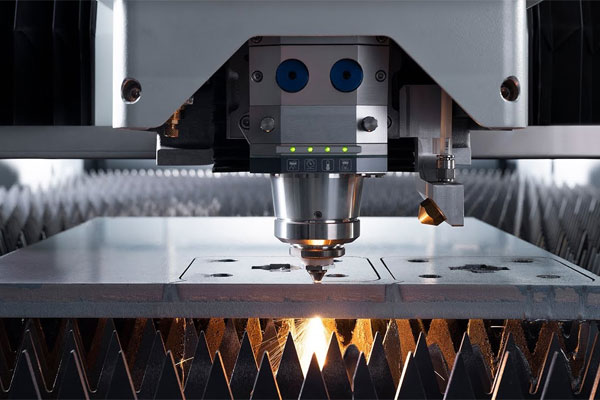
Laser Cutting
- Utilizes a focused laser beam to melt material.
- Best for thin to medium (20 mm max thickness) materials.
- Clean edges, minimal post-processing.
- Extremely precise with a narrow kerf (0.1~0.3 mm).
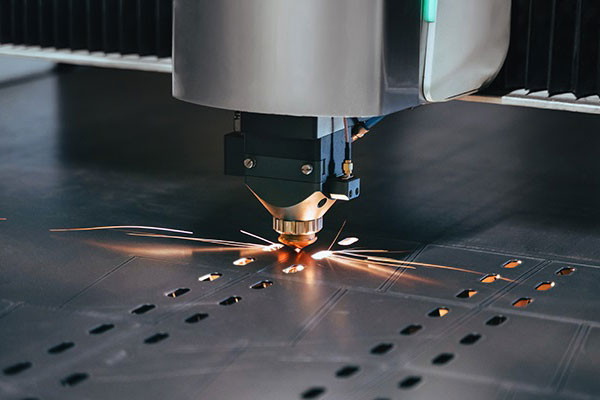
Plasma Cutting
- Use plasma ionized gas to melt and blow away the material.
- Best for thick (50 mm max thickness) metal plates.
- Rougher edges need post-processing.
- Moderate precision with a wider kerf (1~3 mm).
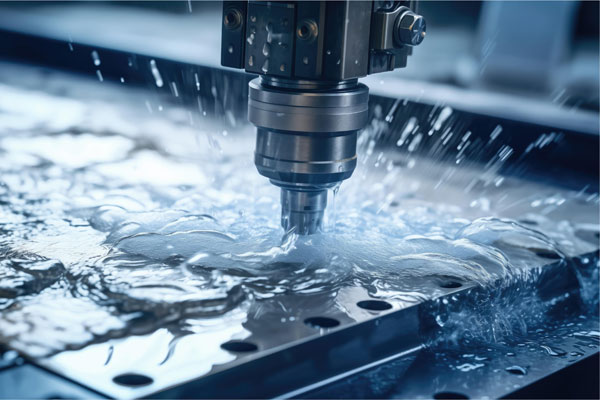
Waterjet Cutting
- A high-pressure waterjet stream cuts through the material.
- Best for cutting thick (>200 mm) or heat-sensitive metals.
- Excellent, smooth edge without needing post-processing.
- High precision with a narrow kerf (0.5 mm to 1 mm).
Quality Controls
For sheet metal cutting, implementing quality control is essential to ensure accuracy, consistency, and meeting our customers’ required specifications.
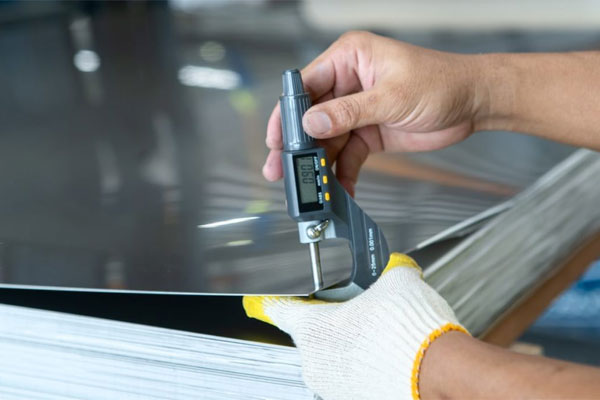
Material Inspection
- Ensure that the sheet metal material matches the specified type, grade, and thickness.
- Check for defects such as warping, cracks, or surface contamination before cutting.
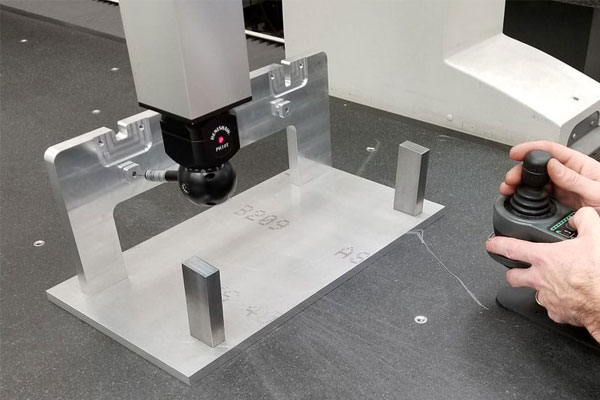
Dimensional Accuracy
- Verify the cut dimensions align with design specifications using micrometers and CMMs.
- Maintain tolerances according to industry standards like ISO 2768 or custom specifications.
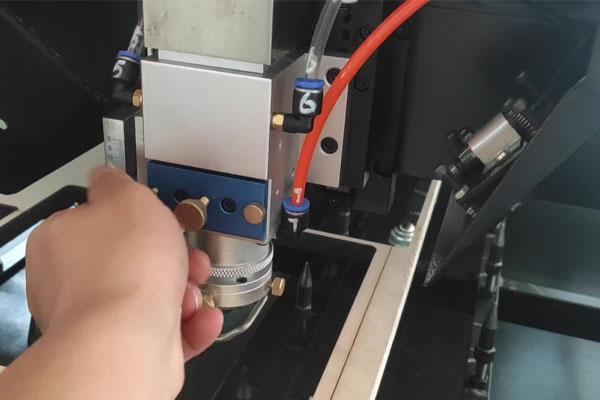
Equipment Calibration
- Calibrate cutting equipment, such as CNC laser cutters and plasma cutters to ensure precision.
- Perform trial cuts to confirm equipment settings before large-scale production.
Post-cutting Process
For sheet metal cutting, the post-cutting process is crucial for ensuring the quality and precision of the finished parts and ready for subsequent manufacturing stages.
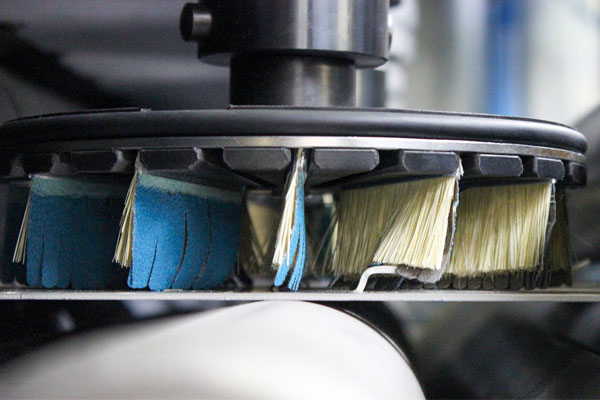
Deburring
This involves removing sharp edges, burrs, and imperfections left from the cutting process. It can be done using various methods like hand tools, rotary tools, or automated deburring machines.
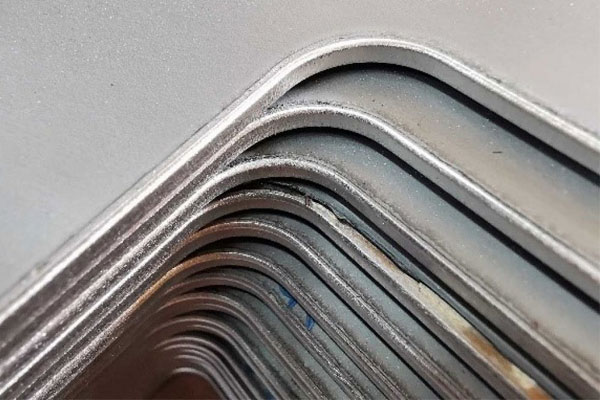
Edge Treatment
This step smooths the edges to improve safety and enhance the aesthetic quality. Edge treatment can be done through processes such as sanding, grinding, or applying edge seals or coatings.
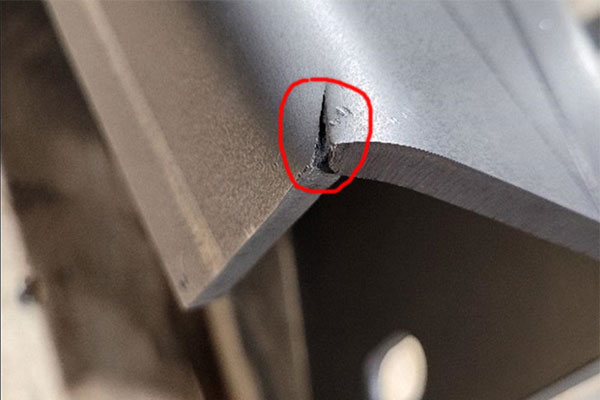
Inspection
Conduct visual inspections and use non-destructive testing methods (such as dye penetrant testing) to detect cracks or internal defects. Check for flatness and warping after cutting.
Sheet Metal Materials
Each metal material presents unique challenges and benefits for sheet metal cutting. The choice of cutting method and settings will depend on the specific material properties and desired outcome.
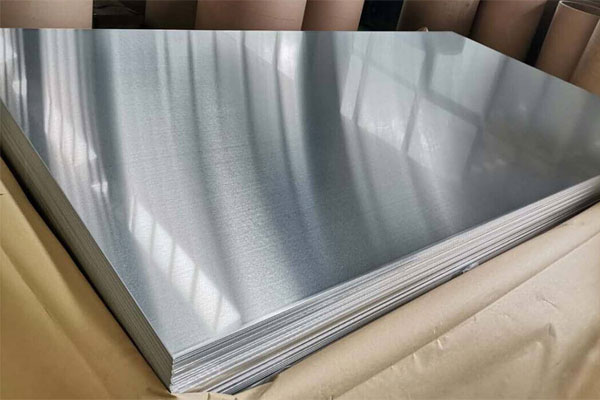
Aluminum
Laser cutting gives precise edges for thin aluminum, while waterjet cutting prevents heat distortion on thicker sheets.
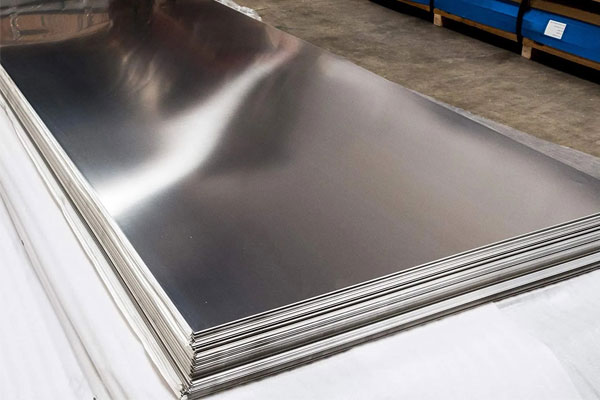
Stainless Steel
Laser cutting suits thin stainless steel with precision; waterjet cuts thicker sections without heat damage.
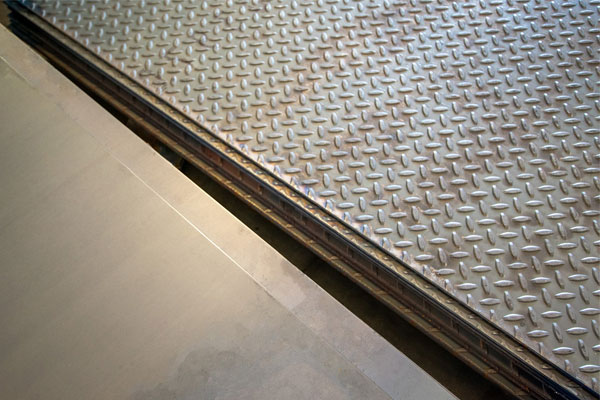
Galvanized Steel
Plasma cutting suits most galvanized steel thicknesses, while laser cutting excels in thinner sheets with intricate details.
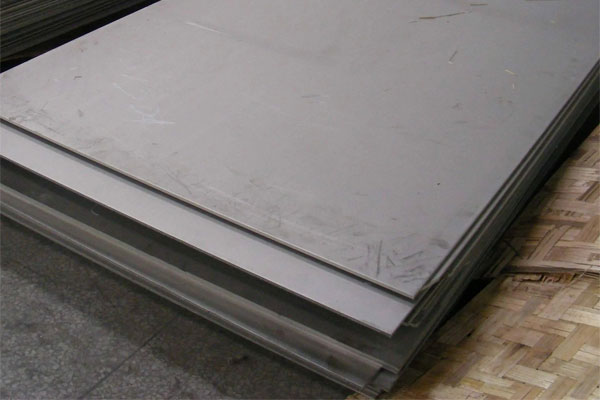
Titanium
Waterjet cutting is the best choice, avoiding heat-affected zones and maintaining structural integrity in titanium sheets.
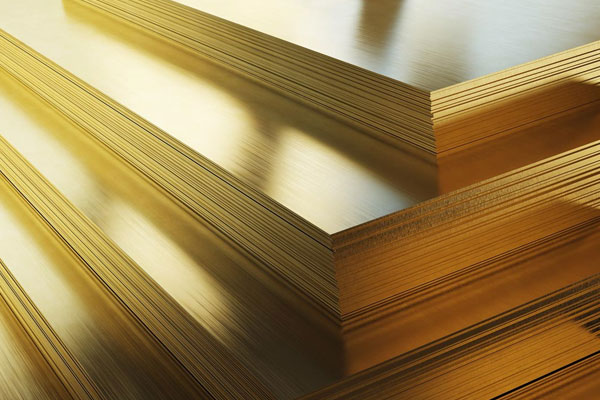
Brass
Laser cutting is ideal for brass, ensuring clean edges without oxidation, suitable for thin to medium sheets.
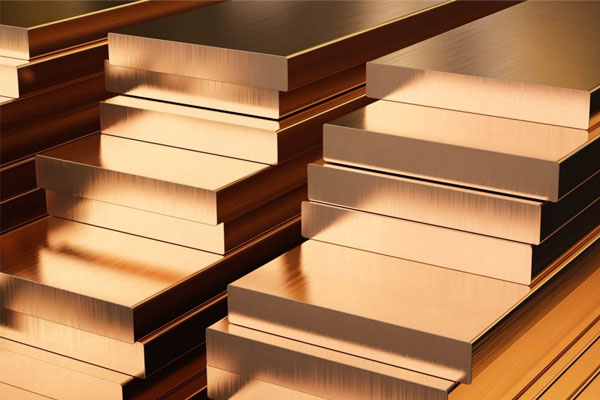
Bronze
Waterjet cutting is optimal for bronze, offering precise, cold cutting without material deformation or discoloration.

Copper
Laser cutting excels in thinner copper sheets. Waterjet cutting is recommended for thicker sheets to avoid thermal issues.
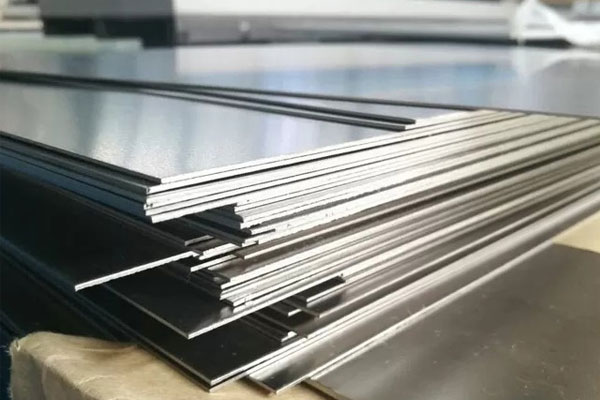
Nickel
Waterjet cutting is best for nickel, ensuring clean cuts without thermal distortion, especially in thicker materials.