Sheet Metal Bending Service
- Sheet metal bending is an essential process in metal fabrication, the goal is to change the geometry of the metal sheet by applying force, creating angular or curved features.
- We specialize in bending metal sheets and plates into V, U, Z and custom shapes using a range of advanced bending techniques with minimized springback and optimized bend radius.
- Various Bending Techniques
- Strict Quality Control Processes
- Maximum 60mm Bending Thickness
- Maximum 1000 Tons Bending Capacity
- ±0.01"(0.25mm) Linear Tolerance
- ±1 Gegree Angular Tolerance
- Accurate Bend Allowance Calculating
- Custom Bending Solution
Our Bending Techniques
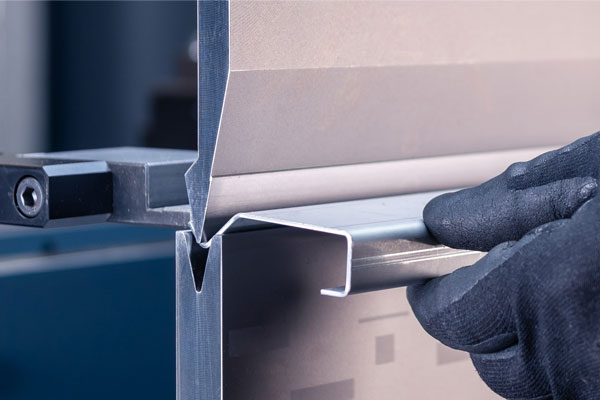
Air Bending
- The punch doesn't touch the bottom of the die, allowing slightly springback.
- Highly versatile, capable of achieving different bend angles with the same tooling.
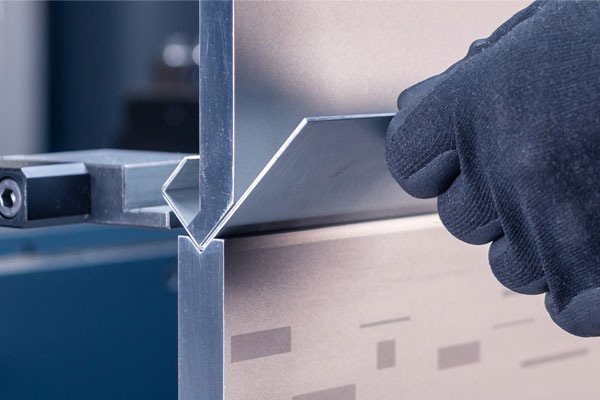
Bottom Bending
- The punch pushes the sheet metal into the bottom of the die, with minimal springback.
- Provides accurate and consistent bends, with tighter angle control than air bending.
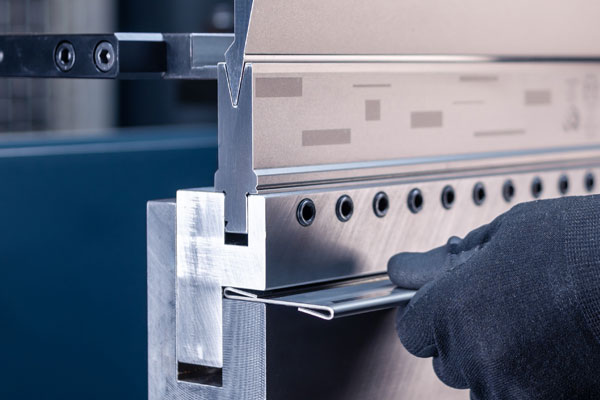
Hem Bending
- The sheet metal is folded onto itself to create a hem, either completely or partially.
- Ideal for creating smooth edges, improving strength, and enhancing safety.
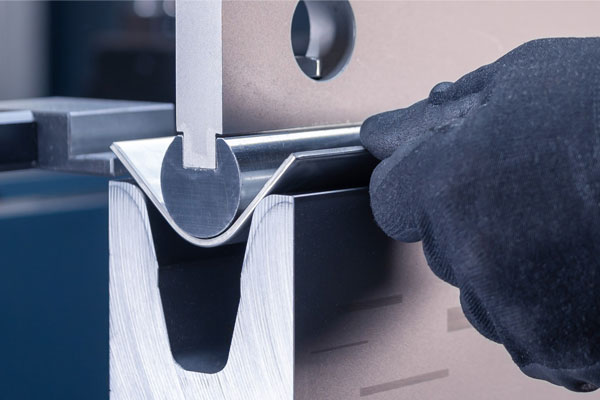
Large Radius Bending
- Produces larger curves or radii than traditional bending methods.
- Ideal for applications needing softer curves or when working with thicker metals.
Shapes That We Can Bend
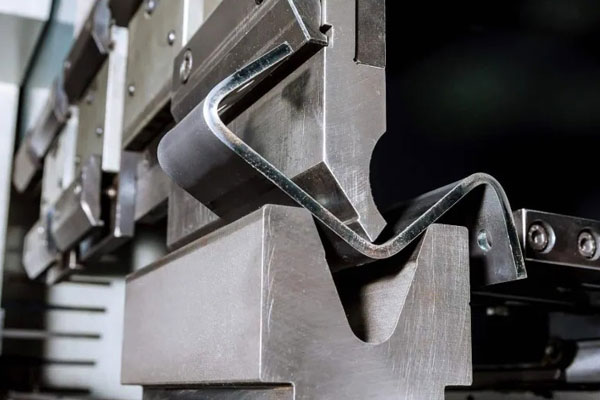
V Bending
- The sheet is pressed into the die, creating a precise V-shape.
- High precision and repeatability.
- Commonly used for creating brackets, channels, and various enclosures.
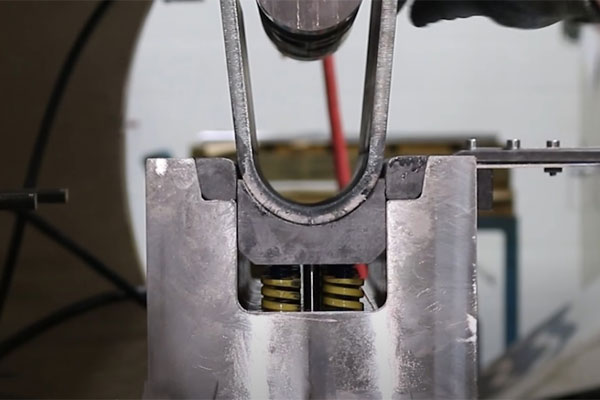
U Bending
- The sheet is bent over a U-shaped die to achieve this shape.
- Provides a consistent bend radius.
- Often used in the manufacturing of parts requiring strong structural integrity.
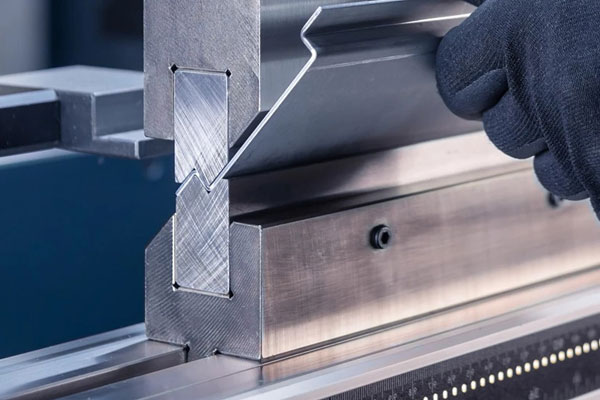
Z Bending
- Bending the sheet into a zigzag pattern, creating a Z shape.
- Allows for multiple bends.
- Frequently used in architectural components, decorative panels, and structural elements.
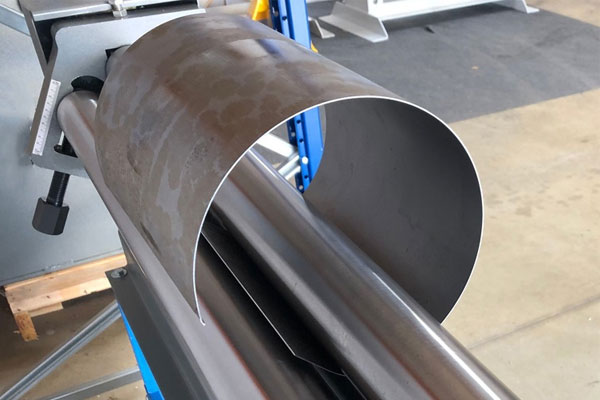
Roll Bending
- Feeding the sheet metal through rollers to achieve a curved shape.
- Ideal for creating large-radius bends.
- Common in producing cylindrical shapes, pipes, and curved panels.
Our Bending Quality Controls
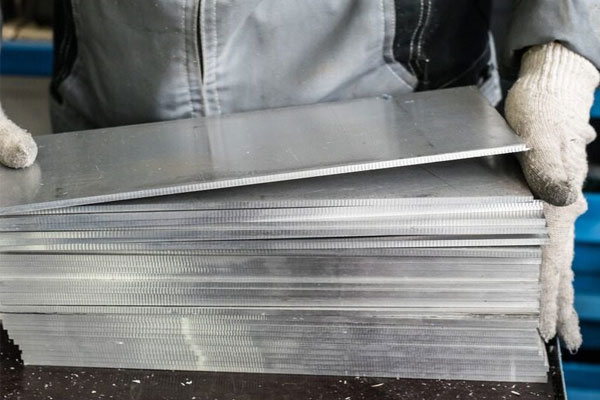
Thickness Consistency
Ensure the material thickness remains consistent throughout the bending process, particularly at the bend areas where deformation may occur.
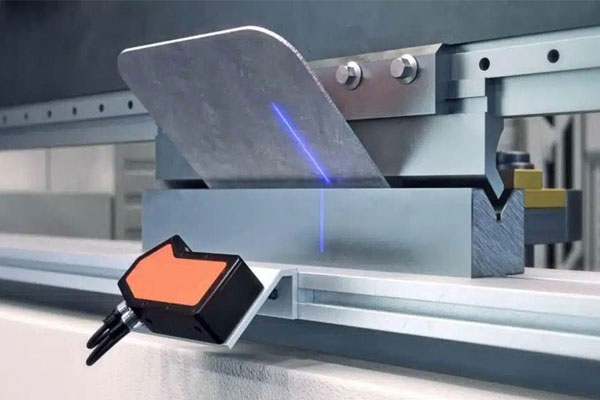
Angle & Radius Inspection
Ensure the bend angle meets the specified angle using angle gauges, and the bend radius adheres to the specifications to prevent cracking or weakening.
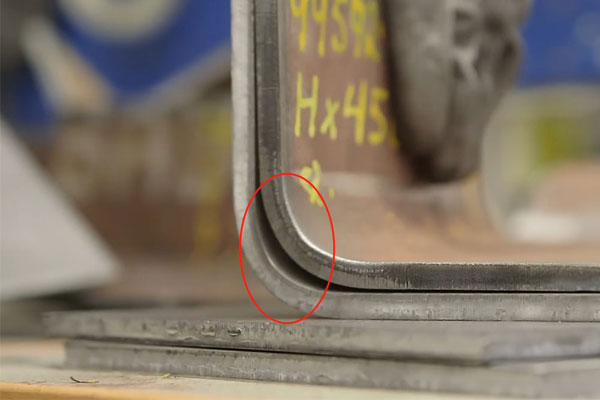
Springback Compensation
Calculating and compensating for the spring back effect during the bending process to ensure the final shape meets the desired shape and dimensions.
Common Materials For Bending
Aluminum | 5052 | 5083 | 6061 | 7075 |
Stainless Steel | 301 | 304 | 316/316L | |
Brass | C27400 | C28000 | C36000 | |
Copper | C101 | C103 | C110 |
Accurate Bend Allowance Calculating
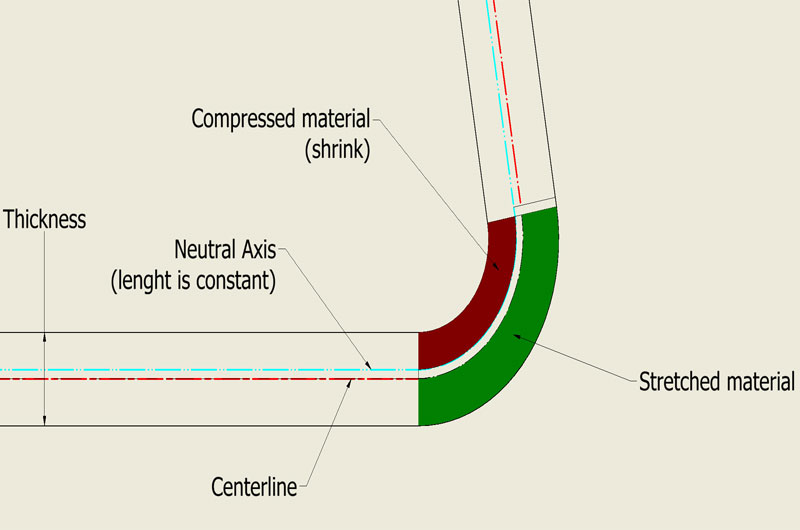
- The sheet metal bend allowance formula is used to calculate the length of the flat material required to form a bend with a specific radius.
- The bend allowance accounts for the stretch that occurs during bending, which is crucial for determining the blank size before bending.
The bend allowance formula is π/180×A×(R+K×T).
- π = 3.14159
- R = Bend radius (the inside radius of the bend)
- T = Thickness of the material
- A = Bend angle in degrees
- K = K-factor (A ratio that accounts for how much material stretches. It's typically between 0.3 and 0.5.)
- Example: For a bend angle of 90°, a material thickness of 2mm, a bend radius of 5mm, and a K-factor of 0.4, the BA= 3.14159/180×90×(5+0.4×2) = 9.11mm.